Making metal parts means working in an industry with slim margins. While other companies often cut corners in an attempt to stay profitable, GH Metal Solutions has taken a different approach, offering a full range of solutions all from the same facility.
GH Metal Solutions sees safety as a long-term investment and not a threat to the bottom line. They have several training programs to ensure employees can perform their job functions safely. They crosstrain several departments to improve efficiency and safety awareness throughout the facility. And they have taken an advanced approach to injury prevention by using SafeStart to deal with human factors.
The Alabama-based company discovered that investing in SafeStart would pay off by reducing the number of recordable incidents. But they didn’t expect the boost in quality, productivity or morale they also received.
Employees at every level have benefited from SafeStart. From better performance to fewer injuries, here’s what the people at GH Metal Solutions have to say about SafeStart.
Edwin Stanley
Vice-President of Operations
We implemented SafeStart with direction from our corporate parents. They introduced us to it and it’s been very successful for us. We’ve been consistent with the implementation and the results have shown that it’s made a difference.
Our incident rate dropped dramatically—it’s decreased by 61%. Our quality has also gotten much better. Our defects have also been reduced, and the timing would suggest that SafeStart had some influence on that.
We track defects per million (DPM) and that’s been cut by 44%. Our customers expect quality parts on time and there’s a cost to us for poor quality. So certainly if we can reduce rejected parts then it saves us a lot of money.
A training program cannot be effective if the end user doesn’t see the value in it. GH Metal Solutions’ safety program did a great job at covering general topics but it didn’t directly appeal to employees. SafeStart changed all that.
Brad Scott
General Manager
We were looking for a way to take our safety to the next level and I thought SafeStart was a pretty good fit. I loved the fact that it was easy, something you could take home to your family. I thought the guys would be interested in that—and they were.
SafeStart has also given us a common language to talk about safety. We talk about complacency, we talk about rushing, we talk about fatigue, things that weren’t on the tips of our tongues before. You hear guys talking about it on the floor every day.
I’ve even had guys on the floor walk up to me when I’ve made a mistake—stepping across a pallet or something—and say, ‘You realize you just did something you shouldn’t do.’ And then we talk about it through the steps of SafeStart. SafeStart has changed the way we look at safety here.
You don’t need to be engaged in extremely dangerous tasks to suffer an injury. Because the work at GH Metal Solutions is often repetitive, employees were operating on autopilot. One benefit the company has seen from SafeStart is increased awareness and a lot less complacency.
Tony Kirtland
Press Brake Operator and SafeStart Trainer
It’s helped me greatly in the job I perform on the floor. As a press brake operator there’s hazards around every corner. SafeStart helped me realize that my biggest obstacle was complacency.
Because some days you may run the same part all day long and it’s easy to take your mind off what you’re doing. So I catch myself paying attention to the amount of hazardous energy around me.
Safety training often takes on a negative tone, blaming workers for mistakes instead of providing corrective action to improve future performance. It also doesn’t deal with why these mistakes keep happening. For tunately for GH Metal Solutions, SafeStar t directly addressed defects and injuries caused by behavior.
Karl Laws
Safety Manager
SafeStart is a great way to give employees, supervisors and managers the ability to understand our behavior and how it can contribute to an accident. It also provides the skills to look at situations and to do something about it without threatening language.
We had a record year for quality and production as well as a record safety year last year. SafeStart has given us the ability to get to the root cause of errors and to understand human behavior. It helps us understand that we all make mistakes, we all have moments when our eyes and mind are not on task, when we get complacent with the situation. And the solution is the same for all of us too. That common ground is the key to making this program work.
One of the biggest challenges in a safety program is getting people to report problems—especially close calls. It’s hard enough to admit you made a mistake when an accident happens, and to admit you narrowly escaped a potentially disastrous event that was entirely your fault is even harder. That’s why SafeStart creates a culture of learning from mistakes.
Jake Pinholster
Training Manager
I thought the SafeStart training was amazing. It’s a challenge to make safety exciting sometimes but I think the buy-in with SafeStart was really good. It’s a simple program. It’s so repetitive that it becomes memorable. The training sticks.
One area we’ve improved the most is close calls— actually reporting them and having the confidence to say ‘this almost happened’ or ‘look how close this was because of this.’ It’s been a great opportunity for us to learn from each other and to learn from our mistakes, to learn from our own complacency. When the guy beside you says something almost happened to him, it’s a great opportunity for everyone to learn.
Before SafeStart, employees at GH Metal Solutions were receiving training but there was no way to measure if any of the material was being retained. Now, all you need to do is walk around the plant and it’s evident that SafeStart has led to a safer and more proactive environment.
Jeremy Cowart
Quality Assurance Inspector
In the 13 years I’ve spent at this company, I’ve seen a lot of safety programs come and go. But I quickly realized that SafeStart was a lot different than the programs I was used to.
I hear people using the SafeStart lingo all the time to remind fellow employees to keep their mind on task. It’s important because if you got a guy paying more attention, keeping his eyes and mind on task, not only is that going to help with safety but it’s going to help him with what’s he’s working on. He’s going to pay a lot more attention to what he’s doing all around.
I’ve noticed that a lot of people now pay attention to their co-workers more often. And they feel they can go to them and say, ‘Hey, you may want to rethink the way you’re doing this because that could potentially get you hurt.’ I think they receive it well and they look out for each other a whole lot more.
Everywhere you look at GH Metal Solutions you can see workers whose safety behavior has been transformed by SafeStart. People are taking responsibility for their own safety and they’re embracing SafeStart concepts—and as a result they’re much safer.
Gary Whitmore
Quality Assurance Technician and SafeStart Trainer
I’m a trainer so SafeStart’s really made an impact on me. I used to be complacent while driving, especially around forklifts. A lot of times I would never stop to look before I turned, and I’d have 25 other things going through my mind while driving. My mind wasn’t on task. SafeStar t really brought me to thinking a different way about what I was doing.
Now, I think our complacency is still there, because we’re human. But in this plant, we’ve been made more aware of it. We have a lot of people driving on the forklift, and prior to SafeStart some of our forklift operators had a propensity to approach stop signs and blind spots in a casual manner.
But now you can hear the forklifts throughout the plant. They stop, they sound their horn. And they’re looking out for you. We’ve also encouraged pedestrians to make eye contact with the forklift driver.
We’re living proof that it works. If you look at our statistics from where we were to where we are now, the record speaks for itself.
Full Video Interviews
This case study is an excerpt from a series of interviews with employees at GH Metal Solutions. Watch the video case study to hear about the firsthand experience of implementing.
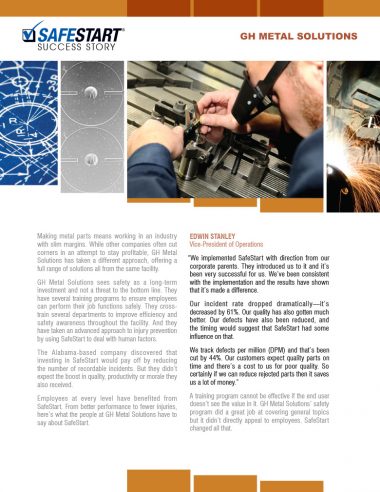
Get the PDF
You can view or download a PDF of this case study using the button below.