This article by Kelley Norris appeared in the
October 2015 issue of Occupational Health & Safety
Everything is bigger when your organization operates on an international scale—your workforce is diverse, your clients are spread across multiple time zones, and your safety system is a complex network of organizational practices and site-specific programs. When implementing a company-wide safety initiative at multiple sites around the world, there’s a lot more to do than simply choosing a training vendor with international experience and letting them handle the rest.
Challenges to rolling out a program on a global scale include language, internal and external cultural differences, varying degrees of safety management maturity at the site level, and inconsistent levels of commitments to employee safety throughout the company. If the program you’re implementing deals with human factors or awareness training then how you deal with these issues can play an especially prominent role in the success of your rollout. A good vendor can help with these issues but ultimately it’s up to the company purchasing the initiative to solve them.
If you’re charged with implementing a new safety program throughout your organization, selecting a vendor to partner with is only the first step. Once you’ve identified your goals and objectives, created a short list, listened to their pitches, run a test pilot or two, established your budget and made your choice—that’s when the real work begins!
1. Set realistic goals
I’ve had many conversations with clients about their big ideas for a global implementation: one price, one rollout, multiple locations, consistent implementation logistics, everybody on the same page at the same time and speaking the same safety “language”. It always sounds ideal, and they speak about it in such euphoric terms—then reality sinks in.
Cross-border safety implementations are almost always more complicated endeavors than initially anticipated, and the sheer manpower alone that’s required to accomplish a full company rollout can be staggering. If you’re not careful, the task of implementing your new safety initiative can end up being a distraction that hinders progress you might have made with a more systematic approach.
You need to set realistic expectations for what you can achieve and must recognize that you can’t implement at every site at the same time. The goal of any safety program is to change behavior and it takes time for employees to fully adopt new safety skills.
I always recommend that clients take manageable steps by implementing a few sites at a time. It’s like the old saying about eating an elephant—even though it’s big, you still finish swallowing one bite before taking another. The same goes for training. Initially rolling out training at a small number of sites allows you to learn lessons from any issues that arise, giving you the opportunity to correct them before they affect the entire rollout.
Bottom line: The best way to implement a multi-site rollout is to take a patient and systematic approach.
2. Establish readiness criteria
Using readiness criteria is one of the best ways to decide which sites are best suited to participate in an initial rollout and which aren’t yet prepared for a new safety initiative.
One large pharmaceutical company we work with uses an assessment tool to determine readiness. In addition to evaluating past experiences with leadership involvement and the site’s ability to maintain an ongoing process, this tool helped them to determine when a location was ready for the new initiative. This approach also allowed them to identify any gaps that might compromise the success of the initiative before they became an issue.
In other cases, corporate safety managers use a cultural assessment tool to determine which site is primed to implement. I’ve also seen clients identify sites that have made temporary safety gains in the past but the injury rate has slowly returned to higher levels.
Establishing which sites are most ready will help you safeguard the implementation and prepare the ground at future sites to give you the best chance at success.
Whatever criteria you use, the goal is to look at culture and find sites that already have a well-developed safety management system. See where on-site leadership is in the best position to support the new initiative and where implementation is likely to be the smoothest. Early victories will help sustain the initiative through any unexpected rough patches down the road.
Bottom line: Partner with your vendor to create/use a readiness tool to help you prioritize sites.
3. Create a stewardship team
A stewardship team can be your eyes and ears on the ground, keeping you informed of the progress and challenges experienced in different regions. Perhaps more importantly, this team is responsible for maintaining the integrity of the initiative.
The team should be tasked with establishing a protocol that consists of lessons learned from pilot programs and the advice of your vendor (they should be experts you can rely on). This group is also responsible for resisting the temptation to cut corners or rush the implementation, and for working with sites from different regions to understand their particular needs and challenges—and then finding solutions that will not compromise results.
The group in charge of the program’s stewardship can also be asked to share early successes throughout the organization, which can help sustain the initiative’s momentum and cast it in a positive light for sites that have yet to implement the new safety program.
This is not a one-person job. Stewardship requires a set of members who all have the same vision and commitment. In my experience, one thing most successful clients have in common is a stewardship team made up of representatives from every major geographical region in the company; these teams make decisions collectively and then each member takes responsibility for executing the plan in their region.
Bottom line: Create a trusted team to maintain the safety initiative’s integrity.
4. Plan for the future Any global project requires a long-term vision.
These types of initiatives can—and should—leave a permanent mark on your company and its greatest asset: the people who work there. But for a new global safety program to achieve its potential, you must plan for an integration that will take years and then support it along the way.
Any successful safety management system has many components and takes into account the unique factors of every different site. As this article has outlined, there are numerous challenges to implementing even modest new initiatives on a global scale. Crafting a long-range plan and then regularly re-evaluating the initiative and making adjustments along the way is essential for the ultimate success of any program.
You should always be planning for the next site implementation or a future sustainability initiative. The biggest mistake I see in global safety implementations is that stakeholders fail to account for the full length of time required to integrate the new program at every site.
Bottom line: Be committed to the long haul.
Kelley has dedicated the last 17 years of her career to working with a team of 25 industrial consultants to help international clients improve safety systems and achieve long-lasting injury reductions.
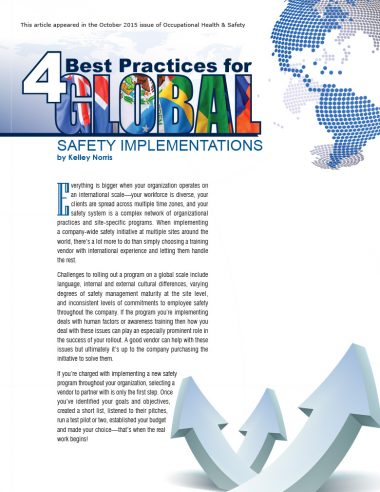
Get the PDF version
You can download a printable PDF of the article using the button below.