By Gary A. Higbee, EMBA, CSP
How “good” is your safety program?
Good question. But a lot trickier than you might think. Lots of people think that it’s a numbers game. If I don’t have a lot of injuries and illnesses, my program must be good. If I do, then it must be bad. But equating the number of accidents and illnesses with the quality of the safety program is confusing cause and effect. It also overlooks the role of luck—good and bad—in workplace health and safety.
The journey to attaining world class safety performance starts with a clear understanding of where you have been, where you are today and where you are going if nothing changes. Then you can determine the changes that need to be made and the path that will get you to your goal. Below is a brief description of each stage of the journey. Remember that you are not alone others have taken the journey before you. Each organization will fit into one or a combination of two stages.
Description of each stage:
- Realization
Organizations in this stage see skyrocketing injury rates and “through the roof” worker compensation costs are prompting management to do “something”. Governing bodies often conduct audits and identify areas of improvement to meet minimal compliance requirements. Consequences to non-compliance can be very costly. Financially the direct costs of loss time injuries are affecting overall profitability. Companies at this stage are at a legal risk and employees have a high risk of injury. - Traditional
Companies at this stage of the process are still at risk of injury but are probably at a point where they are protected from most legal risk by Worker’s Compensation sole remedy laws. There is minimal legal risk at this stage. Priorities are placed on developing policies and procedures and the education process begins. They haven’t succeeded in changing behaviors yet and workers and management are still apt to do what is convenient for them. An increase in production and overhead costs results from having identified at risk conditions and taking appropriate steps to engineer out the hazards. Machine maintenance and repair, shielding and guarding derive from a reactive management approach – “we’ll fix it when it’s broken”. Most stop their development at this stage. - Observation (process)
Management initiates an observation based safety program in addition to the traditional program and spends more time on the production floor or the worksite “observing” for hazards with compliance in mind. Concern for compliance is at the forefront of their minds and more adequate record keeping becomes a priority. Management drives the improvement process. There is little to no employee involvement at this stage because the observations are performed by management employees. - Empowerment
Management and employees share in the responsibility of understanding risks, preventing injuries and are jointly accountable in the education process. The employees have gained confidence in the management group that safety is a core value of the organization. Employees drive the improvement strategies and all are committed to company and team goals. Not only is the company continuing to decrease injuries in the workplace, increasing awareness of risk factors through employee observations the employees are developing “habit strength” for effective safe behaviors. Financially the organization is reaping the benefit as a result of a continuous decrease in loss time injuries and is experiencing a competitive advantage as monies are being allocated to other areas of the organization. Productivity and quality is also improved. - Utopia
The company’s safety culture is self-sustaining and developing. Employees are looking out for each other and peer to peer safety interventions are a normal part of the operation. The company is progressive in its approach to safety and has become the benchmark by which other companies in the industry measure their safety performance.
The illustration below will help you visualize where their company is and how it compares to others. The larger the area of the diamond the more companies in that stage. For example the safety performance of most companies in North America can be found in stage two.
I wrote about the five stages over twenty years ago. While I haven’t changed my mind about the progression I have found an issue that needed to be dealt with. The Habit Strength behaviors talked about in the fourth stage work under normal situations but under stress habits can go in a heart beat. For example: I was performing an audit at a manufacturing facility. During the audit I noticed one forklift operator was particularly good at his craft. He always wore his seatbelt and never set a load at the production line without clearing the employees and when he entered a trailer at the loading dock he always inspected the trailer and assured the wheels were caulked. He just did everything right. In the afternoon I noticed some extra activity on the production line. The line was going down because of a missing part that was stored outside in a trailer that was stuck in the snow. The assembly line employees were incentive workers and they didn’t want the line to go down because it would cost them money. Just 30 seconds before the line was to go down the truck was freed from the snow and backed to the dock. The forklift driver I had been admiring jumped on his forklift drove into the trailer and got the load. He placed the load on the line and everyone cheered. The problem is he didn’t fasten his seatbelt, the trailer was not caulked and if the semi driver would have pulled foreword to reset the trailer who knows what might have happened. His habit strength was lost in an instant.
The 3 signs of a top-notch safety program
Today I have simplified things a bit. I’ve seen all kinds of safety programs and in my opinion, there are three things all world-class programs have. How many of them does your program have? If you have all three, it’s a pretty good sign that you’re doing things right.
- First you have to have a strong traditional safety program. This includes written programs, policies and procedures and how those policies and procedures are followed. You find out how good your traditional safety program is by auditing to set standards. You can do this internally or you can have someone from outside audit your program. It is a simple way to look at what you say you do and checking to see if you actually do it. Most of us have a lot of work to do to just get our traditional programs up to snuff.
- Second you need some type of observation program. Companies with first rate safety programs introduce an observation process, with management and workers’ input, to watch out for at risk behaviors. There needs to be teamwork. The best companies, safety-wise, encourage workers on the floor to perform safety observations on a peer to peer basis and also accompany the supervisor and safety director on their rounds. Those observed committing at risk behaviors aren’t disciplined but are part of a discussion on have to correct the observed at risk behavior. This process develops “habit strength” for safe behaviors. This is not an audit program but a behavioral observation process that includes both employees and management in the process. Observing employees to assure they know how to do their job and have the tools necessary to perform their tasks safely. Your looking for gaps in the system and at the same time your reinforcing safe behaviors and intervening when at risk behaviors are observed. See stages three and four above.
- Third employees need advanced safety skills and safety awareness. In order for all the aforementioned points to be truly successful, employees need to be taught the right “skills” in order for them to be able to keep themselves safe when the system breaks down. Without safety skills the system will continue to fail under stress because some will loose the habit strength developed through observations. This is what was missing in the five stages. We don’t expect that if a would-be golfer reads the golf rule book that he will automatically be a better golfer. They need practical, relevant and easy to understand skills to manage themselves effectively.
World class safety performance is not just the dream of some wide eyed college graduate or recently appointed Safety Manager. World class safety performance is a very real possibility. Wouldn’t be wonderful if your company was the benchmark company by which others in your industry measure their safety performance?
Gary is an expert in safety management systems and organizational change, he is a two-time past president of the Hawkeye Chapter of the ASSP and past Regional Safety Professional of the Year. In 2010, Gary was awarded the Distinguished Service to Safety Award, the top individual safety award from the NSC.
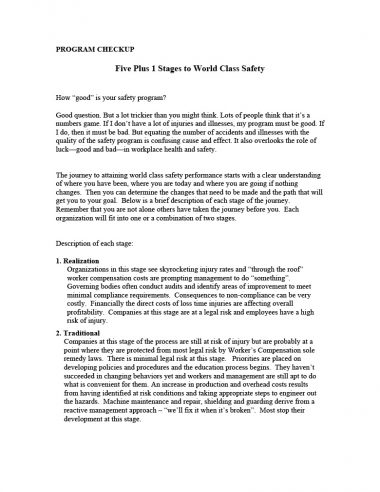
Get the PDF version
You can download a printable PDF of the article using the button below.