This article by Don Wilson was published in the
ASSP’s April 2016 issue of The Compass
Companies increasingly view the accumulated skills and intellectual capital of their workforce as a major resource and, in many cases, as a competitive advantage. If you ask a group of CEOs what their business’s biggest asset is, one of the most common answers is: “It is our people that make this company a world leader in our field.”
To safeguard that leadership position, companies takes steps to ensure that their employees are kept satisfied, safe at work and healthy.
To keep employees happy and satisfied, companies offer competitive wages and benefits. To help keep them healthy, employers offer world-class health insurance and additional paid programs such as smoking cessation programs or subsidized gym memberships.
But what role does traditional workplace safety management play in protecting workers from unintentional injury and death, and how is that role changing in the modern world?
Many safety systems are not particularly efficient at protecting workers. Most corporate safety programs focus exclusively on workplace safety, which means that for the 8 hours a day someone is at work they have the benefit of a safety manager, PPE and other safety measures.
Unfortunately, the vast majority of injuries and accidental deaths occur outside the workplace. A key issue that many employers face today is how to use their current safety management system to protect employees 24/7.
This article demonstrates that businesses will increase productivity and reduce costs by including off-the-job safety in their safety program. It also outlines how corporate leaders can take proactive measures to protect their workers at work, at home and on the road.
The majority of injuries and accidental deaths occur outside the workplace, and a key issue that many employers face is how to use current safety management systems to protect employees 24/7.
The Importance of Universal Safety Skills
Even though hazards vary from one workplace to the next, and from work to the road and home, the basic causes and patterns of injuries remain constant, and lack of knowledge about hazards is rarely a factor. In fact, most people are injured despite knowing about a hazard. So what causes someone to come into contact with a hazard they are aware of? The answer is human error.
A universal pattern of mental states causes people to make one of four errors. These four states and four errors combine to cause more than 95% of all unintentional injuries (Figure 5). This state-to-error pattern is universal. Not only do rushing, frustration, fatigue and complacency increase the risk of injury, they also increase the potential severity of potential injuries.
One of the reasons traditional safety programs cannot effectively combat off-the-job injuries is because they are only relevant in a specific workplace context. Therefore, solutions to limit injury-causing errors must be as universal as the errors.
Statistically speaking, workers are now much more likely to get injured at home or driving to work than on the job.
Fortunately, it is possible for people to improve their safety awareness, skills and behavior to make fewer errors and reduce their risk of injury. In particular, there are four skills that have been demonstrated to provide lasting improvements to employee safety:
- self-trigger on the state
- analyze close calls and small errors
- look at others for risk patterns
- work on habits
These four techniques help workers to:
- become more aware of when they are in one of the four states to reduce the chances that it will lead to an error examine the small errors they make to learn lessons that will help them avoid making larger errors that might lead to more serious injuries
- recognize the dangerous behavior of others and use it as a reminder to avoid similar risk patterns in their own behavior
- develop these and other safety skills through constant practice and habit formation
These skills are transferrable to any situation and they have a much greater reach than the traditional hierarchy of controls. While these methods of strengthening safety awareness can be extremely effective, simply being aware of them is not enough to prevent injuries. To truly benefit from these new skills takes practice at work, at home and on the road, which also takes motivation.
Figure 5: SafeStart State-to-Error Pattern
The Changing Nature of Workplaces & Population Demographics in the Western World
To say that workplaces and the type of work conducted by employees in countries like Canada and the U.S. have undergone a dramatic revolution in the past few decades would be an understatement. One factor influencing this change has been the rise of cheap labor markets in emerging economies. Change has also been driven by the availability of cheaper and more reliable global transportation networks to move goods easily between markets. A third factor is the ability to seamlessly connect engineering and management systems located in high-wage nations (e.g., Canada, U.S.) with manufacturing and service locations in low-wage countries such as China or India via the Internet and telephone. These three factors have led to many low-wage and low-skill jobs that were once the staple of Western economies being outsourced to low-wage regions. As a result, more of the jobs available in Western economies require much higher degrees of skill, education and training (Figure 1).
Throughout the past 50 years countries like Canada and the U.S. have also been undergoing a second revolution: a dramatic decrease in average family size (Figure 2). This bir th rate decrease is now at the point where most Western countries can no longer maintain their present population levels without increasing immigration from countries that still have growing populations.
Unfortunately, while many citizens who live in emerging economies are eager to move to North America, their education, skills and work experience often do not match the skills and education that are in high demand in Canada and the U.S. Given this, as well as the length of time it takes the U.S. education system to produce graduates with the skills and education required for many jobs, employees truly are a company’s most valuable asset—and the hardest asset to replace.
The Changing Nature of Work & Workplace Safety
Automation and regulation during the past century have reduced workplace risk. Vast improvements have been made in workplace hazard reduction and in removing humans from harm’s way with robotic or remotely controlled production systems. At the same time, regulatory agencies (e.g., OSHA in the U.S.) and new due diligence laws (e.g., Bill C-45 in Canada) have helped to bring attention to workplace safety.
Most ASSP members have their workplace safety process efficiently operating well above industry standards with a wellrounded set of procedures, including job safety analyses, engineering, guards and PPE. As a result of this focus on workplace safety, injuries in the North American workplace have slowly but steadily decreased over the past decade.
Statistically speaking, workers are now much more likely to get injured at home or driving to work than on the job. In fact, nearly three times as many workers suffer nonfatal injuries off the job as on the job (Figure 3). For fatalities, the numbers are more stark, with 11 times more people dying from unintentional injuries off the job than on the job (Figure 4).
The nature of work and what constitutes a workplace has also changed. Over the past century, jobs in the Western economy have migrated from being mostly manual to becoming primarily service based. Often, these new, more cerebral jobs can and are being done anywhere and at any time. As employee teams become less centralized in a single workplace, organizations’ ability to enforce safety rules, procedures and regulations has also naturally declined. Gone are the days when an ASSP member’s world was the inside of a factory and every employee worked his/her daily shifts in that workspace.
Companies fail to prevent off-the-job injuries because the methods they use to keep employees safe are effective at work, but they are nontransferrable. Once employees leave work at the end of the day or work remotely, they no longer have their safety manager looking over their shoulder and are less able to rely on the measures designed to keep on-site workers safe. Many corporate leaders also fail to recognize that injured employees present a serious financial cost regardless of whether the injuries occur during or outside working hours.
Figure 1: Metros With Biggest Projected Shortfall
of Mid-Skill Workers in Skilled Trades, Tech & Business/Finance
Figure 2: Projected Population Growth of the U.S.
The Real Cost of Employee Injuries
Most people are aware of the direct cost of injuries, and it is a relatively straightforward task to tally up medical and workers’ compensation costs to determine how much a company has to pay out annually due to workplace injuries.
However, these costs are only the tip of the iceberg. To truly account for the cost of employee injury, it is necessary to consider the financial impact of the following factors:
- time lost from work
- loss in earning power
- lost time by fellow workers
- loss of efficiency due to break up of crew
- lost time by supervision
- cost of breaking in new person
- damage to tools and equipment
- time damaged equipment is out of service
- spoiled work
- loss of production
- failure to fill orders
- overhead costs
- company/worker morale
Figure 3: Off-the-Job Injuries Vs. On-the-Job Injuries
These hidden costs all affect a company’s bottom line regardless of whether an employee was injured at work or at home. If someone gets hurt on the weekend and cannot come into work on Monday, his/her employer is negatively impacted by the worker’s failure to fill orders, loss of team efficiency and more. And if a replacement is hired to make up for the loss in production, the new worker’s inexperience may lead to damaged tools, additional material waste and a general reduction in efficiency.
The real cost of employee injury is not medical claims, but the loss of productive workers and the sizeable financial investment required to hire and train a replacement. It is in a business’s best interest to avoid these costs by protecting employees where they get hurt the most—outside the workplace.
Figure 4: Off-the-Job Deaths Vs. On-the-Job Deaths
Teaching 24/7 Safety
Experts agree that when it comes to influencing change, people need help positively answering two questions. First, people must decide if they think they can do what you want them to do. Second, people must decide if they think it will benefit them personally. Is it easy enough for them to do and is it worth their effort?
A great deal of safety leadership consists of finding ways to get employees to answer yes to both these questions. From a 24/7 safety perspective this means the personal skills, habits and behaviors must be easy to use in their daily life and that people must believe that adopting them will reduce their injuries.
One effective way to engage and motivate employees is to focus on their safety agenda rather than the company’s safety goals. For example, most people are far more motivated to protect their families than themselves, and given the necessary tools almost every employee will teach their family stronger safety skills.
From a company’s perspective, turning each employee into a trainer (even if they are only training their own family) is an ideal outcome. People retain far more information when they actively participate in learning. When it comes to learning the practical safety skills outlined in the previous section, encouraging employees to teach the skills to their families will help them stay motivated, retain more information, be more likely to practice the safety skills themselves and feel more invested in a safety program.
Conclusion
Traditional safety management approaches focus exclusively on measures to reduce workplace injuries. This ignores the fact that people are statistically safest at work and much more likely to get hurt off the job. Additionally, there is a high cost to replacing employees regardless of whether they are on the clock when an injury occurs.
Command and control strategies have little positive effect to improve off-the-job injuries, and it behooves employers to adapt their current safety management system to protect employees 24/7. They can do so by providing workers with skills to increase their awareness and reduce the errors that lead to injuries no matter where they are. If businesses motivate employees by addressing their safety agenda they can effectively influence them to learn skills and adopt habits to reduce injuries. In the process, they will also lower costs and avoid productivity loss.
Don Wilson has more than 25 years’ experience in industrial education, safety and health training, and instructional design. He is a frequent speaker at corporate safety and health meetings, as well as NSC, ASSP and VPPPA conferences.
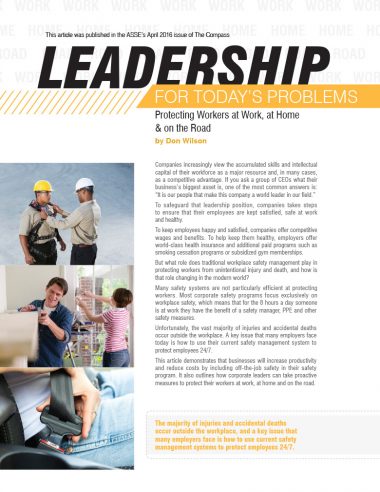
Get the PDF version
You can download a printable PDF of the article using the button below.