Background
As the operating contractor at the Lone Star Army Ammunition Plant, Day & Zimmermann’s (D&Z) primary mission is to load, assemble, and pack ammunition for the United States Army. D&Z, which currently employs approximately 380 employees at Lone Star, had completed 12 months without a lost-time injury. With only 14 OSHA recordable incidents, it seemed as though Lone Star should be content with its exemplary safety record. However, with safety as Day & Zimmermann’s number one corporate value, continued improvement of Lone Star’s safety effort is a top objective.
Training Need
With 30 years of experience in the safety profession, Phillip Haltom, Lone Star’s Director of Safety, Human Resources, Plant Protection and Facilities Maintenance, understands the difficulties associated with maintaining low accident rates. And so does his company. Bill Holmes, President & CEO of Day & Zimmermann’s Munitions and Government Services operating group, tasked facilities within his areas of responsibility to implement a behavior-based safety program at each facility. Even though 44 percent of Lone Star’s employee base has at least 30 years of experience, both Haltom and the company knew there was room for accident reduction.
After researching the market, Lone Star management selected the advanced safety awareness program, SafeStart, because it believed the program would hold employees’ interest and because the training emphasizes safety both on and off-the-job. This workplace-to-home aspect was important to the company because fewer injuries at home translate into fewer days missed from work. And, the use of videotapes and selfpaced exercises with topic discussion was considered to be the best approach to exposing employees to a behavior-based program.
Implementation
A SafeStart implementation specialist was hard at work preparing Lone Star’s trainers for the job ahead of them. Employees at Lone Star began the six week training session with the Unit 1 workbook and attended five, ninety-minute training sessions there after.
Three hundred thirty-six (336) employees—or 98 percent of the total workforce—completed the training. Each classroom session was comprised of employees from different departments throughout the plant. This ensured a highly effective and interactive training experience. Today, the company continues to hold monthly safety meetings to reinforce the SafeStart concepts.
Results
SafeStart is “the most important program we’ve done all year.” That is Haltom’s sentiment after looking back on the effects SafeStart has had on Lone Star’s employees. In addition to creating an increased awareness and focus on safety throughout the plant, according to Haltom, the SafeStart training has had such far-reaching cultural effects that some employees have taken their workbooks home to educate their families.
SafeStart has been a major factor in keeping Lone Star’s workforce focused on safety. With OSHA recordable incidents declining and no lost-time injuries reported, Lone Star employees, using the SafeStart concepts, are working tirelessly to meet the Day & Zimmermann goal of an accident-free workplace.
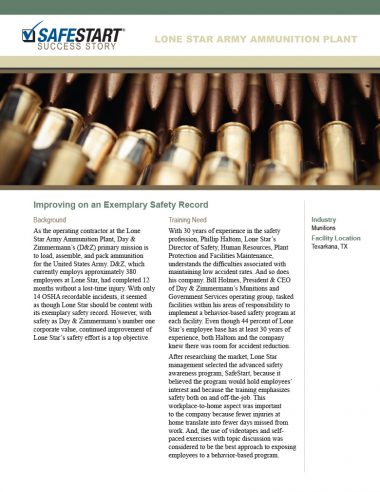
Get the PDF
You can view or download a PDF of this case study using the button below.