Performance Turnaround
Complaints, low productivity, recurring injuries, unhappy employees—management at Plymouth Tube’s Streator mill will recall struggling with these problems all too well.
Plymouth Tube is a family-owned company comprised of eleven autonomous manufacturing plants that produce precision steel tubing and engineered shapes in steel and titanium. Their second-oldest mill is a 100,000 square foot facility located in Streator, IL that produces cold drawn mechanical and aircraft alloy tubing. Notable customers include Stock Car Steel and products made in Streator end up in NASCAR engines and roll cages. The mill also produces tubing for hydraulic and aircraft purposes.
So Plymouth Tube knows a thing or two about performance. Unfortunately, their Streator mill is also familiar with workplace injuries.
For years the Streator mill’s OSHA total recordable incident rate hovered around 7 or 8. This translated to a workers’ compensation premium of over $1 million in 2008 alone. Things only got worse from there and in 2012 when the mill’s OSHA rate reached 13 they knew they needed help.
The Streator mill hired Operations Manager Kyle Roach and tasked him with tightening up safety practices. Kyle reviewed their current safety training and found that while it tried to protect every employee it never resonated with them—and the injury rate steadily increased as a result. What they needed was a safety process that engaged employees and provided lasting results.
Along with rolling out other safety initiatives and engagement programs, Plymouth Tube supported the Streator mill in implementing SafeStart in 2013. The mill has achieved amazing results and their safety turnaround has even caught the attention of other sites in the company.
How did SafeStart help the Streator mill transform their safety performance? It all starts with one of the biggest challenges in safety—employee engagement.
Safety Engagement One Employee at a Time
Safety was always a priority for Streator mill’s management but the policies and procedures they created to keep people safe weren’t actually leading to fewer injuries. Once SafeStart was implemented, one of the biggest shifts Kyle noticed was an increased focus on culture. “SafeStart helped us to make a culture change instead of introducing a bunch of rules,” he says.
SafeStart immediately changed employees’ view of safety, and their eyes no longer glazed over every time a safety concern was addressed. It went beyond creating a common language within their workplace and employees seemed more in tune with what was required to stay safe. All this resulted in increased PPE wearing, better identification of hazards and more safety observations.
SafeStart stood out to employees because it provided skills to keep them safe not only at work, but also when performing non-work related tasks at home and while driving. In short, it appealed to their agenda—and that makes a huge difference. “When you start talking about safety at home, people listen to that,” Kyle says. “It really got their attention.”
And it really works too. Kyle says he knows his employees are using SafeStart at home because they tell him. “I hear a lot of stories from staff about things they’re doing now that they never were before— like wearing hearing protection at home.” Fewer injuries at home means fewer missed days at work. It also has a huge impact on safety behavior on the job. Kyle found that SafeStart training was particularly significant in increasing the interaction among the entire mill, which he says is not an easy feat in this type of environment.
SafeStart helped them break through the communication wall and bridge the gap between management and employees. “I know it takes time to change a culture,” Kyle explains, “but I think we’re heading in the direction where people actually care more, they are more aware of what they are doing and they don’t want to go home injured.”
SafeStart helped us to make a culture change instead of introducing a bunch of rules.
An Impressive Injury-free Milestone
On January 24, 2015, Plymouth Tube’s Streator mill reached a milestone: two years without an OSHA recordable.
This enviable record speaks volumes about how far the mill has come in terms of safety. Before SafeStart, Streator had a recordable rate of 7.33. After implementing SafeStart that number has dropped to 0—and it’s stayed there.
“We had never, ever gone one year without an accident and now we’ve achieved two years,” says Kyle. “So what’s the difference? SafeStart was a big part of that.”
Eight months after reaching the two-year mark the mill’s injury-free streak shows no signs of slowing. Kyle agrees. “We have gone 2 years without an OSHA [recordable injury] and I think we can go well beyond that because of SafeStart.”
That’s caught the attention of other Plymouth Tube sites, which are amazed at the quick decline of incidents at Streator. “We’ve had several mills come to our mill for a meeting to find out what we’re doing,” Kyle says. He’s quick to point out that SafeStart in combination with safety observations has made a huge improvement within the plant.
One of the reasons for the success is that SafeStart is infused throughout the entire workforce and not just hourly workers. Everyone participated in training, Kyle notes, “including the GM, quality department, accounting is going through the units, so we’re all speaking the same language.”
Streator’s safety success has become a benchmark for other Plymouth Tube sites in the company’s corporate-wide drive to help employees keep eyes and mind on task, and stay aware of line-of-fire. As part of Streator’s inclusive safety culture, lessons learned at Streator are eagerly shared with sister mills. “This is the type of culture I was looking to achieve,” Kyle says, “and that is what SafeStart has helped us create.”
We have gone 2 years without an OSHA [recordable injury] and I think we can go well beyond that because of SafeStart.
Injuries are Down, Production is Up
SafeStart’s benefits aren’t limited to safety improvements—and you don’t have to look any further than Plymouth Tube’s Streator mill to see how SafeStart can improve productivity and have a tangible impact on the bottom line.
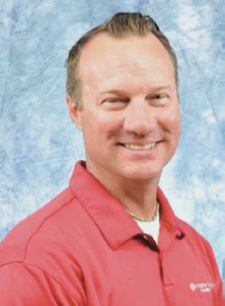
“Our production numbers are up,” Kyle says. “We’re having one of the best years we’ve had in a long time. And it’s not due to sales.”
A reduction in workplace injuries and increase in attention has boosted production. “In years past you had people out due to injury. Now everyone’s here and that has a positive effect,” Kyle notes. SafeStart has helped employees focus on cleanliness and workplace organization, which has improved both safety and productivity.
Kyle summarizes succinctly. “Productivity is up. Our customer complaints are down. And our yield is up.” These improvements represent a substantial financial benefit. A little over two years before SafeStart the site’s workers’ compensation costs were over $140,000. After implementing SafeStart that number is lower. A lot lower.
Life is good. All our metrics are moving in the right direction. Every single one of them has improved.
“Our workers’ compensation is down to zero,” Kyle says. “That’s huge.” It’s also new territory for the mill. “We’ve never been at zero in a single year ever in the history of this company at Streator,” he says.
Kyle is feeling positive thanks to SafeStart’s role in Streator’s dramatic turnaround. “Life is good. All our metrics are moving in the right direction. Every single one of them has improved.”
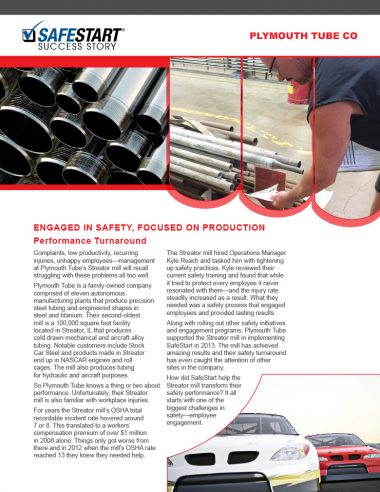
Get the PDF
You can view or download a PDF of this case study using the button below.